COMPUTER AIDED DESIGN, DRAFTING, ANALYSIS & SIMULATIONS (CADDAS) CERTIFICATION FOUR (4) MONTHS PROGRAMME - ONSHORE, OFFSHORE, PIPELINE, SUBSEA & HYDRODYNAMICS 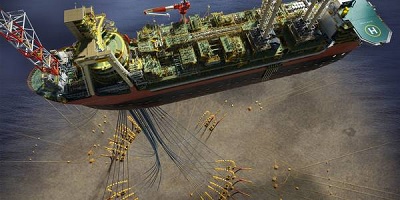
Chess Subsea Engineering Limited, a UK based surface, marine & naval architecture, hydrodynamics & subsea production systems engineering consultancy and research & development company with extensive experience with Floating Production Storage & Offloading (FPSO) unit, Jack-up, Drilling Units, Drillships, Risers and Pipelines is set to train & certify Nigerian graduates and working professionals changing careers intensively within four months (4) in the areas of Pipelines, Onshore & Offshore Topsides Structures, Subsea & Hydrodynamics Engineering using modern Computer Aided Design, Drafting, Analysis & Simulations (CADDAS) software’s with focus on onshore, deep and shallow water project. This four (4) months intensive engineering CADDAS programme has been fully subsidized and offered in accordance to Nigerian Local Content requirements on training and manpower development indigenously.
PURPOSE To develop the highly specialized skills and knowledge in the areas of Offshore & Subsea Engineering Procurement Installation & Construction (OSEPIC). This online or offline CADDAS programme is structured for engineers from any disciplines who intend switching careers and working as subsea pipeline engineers, subsea systems design engineers, subsea reliability engineers, subsea integrity engineers, offshore engineers, offshore project managers & offshore supervisors for local or international offshore and subsea contractors or IOC’s globally.
OBJECTIVE
At the end of the programme participant will be able to function with minimum supervision for IOCs, subsea pipeline company contractor, vendor or installation as a subsea pipeline engineers, subsea systems design engineers, subsea reliability engineers, subsea integrity engineers, offshore engineers, offshore project managers & offshore supervisors
CADDAS Programme is a programme structured to bridge the needed knowledge gap at beginners to intermediate level and gain mastering.
4 MONTHS (17 WEEKS) PROGRAMME OUTLINE
CADDAS 001: OIL & GAS, OFFSHORE, SUBSEA & AUTOCAD 2D ENGINEERING MASTER CLASS
Wk1 - Wk2: COURSE MODULES - Module 1: Introduction to Oil & Gas Engineering
- Module 2a: Introduction to Offshore Structures Engineering
- Module 2b: Fundamentals of Floating Production Storage and Offloading (FPSO) Unit Engineering Design Architecture
- Module 3: Fundamentals of Subsea Engineering
- Module 4: Offshore Hydrography & Site Investigation
- Module 5: Subsea Surveys System Positioning & Metrology
- Module 6: Fundamentals of 2D Drafting Overview with AutoCAD
TECHNICAL WORKSHOPS - CADDAS 001a: AutoCAD 2D Drafting & Annotation Workshop
CADDAS 002: 3D MODELING OF ONSHORE, OFFSHORE & SUBSEA ENGINEERING DESIGN MASTER CLASS WITH AUTODESK INVENTOR
Wk3 - Wk4: COURSE MODULES - Module 1: 3D Modelling Overview of Onshore, Offshore & Subsea Systems with AutoDESK Inventor (SolidWorks Optional)
TECHNICAL WORKSHOPS - CADDAS 002a Case Study: Creation of 2D & 3D Engineering Component Parts with AutoDESK Inventor
- CADDAS 002b Case Study: 3D Components Assembling with AutoDESK Inventor
- CADDAS 002c Case Study: Creation of Annotated Drawing Document with AutoDESK Inventor
- CADDAS 002d Case Study: Creation of 3D Exploded Projection view of an Assembly with AutoDESK Inventor
PROJECT Offshore & Subsea Production Systems & Component 2D & 3D Engineering Design Case Studies
CADDAS 003: FINITE ELEMENT ANALYSIS OF ONSHORE, OFFSHORE & SUBSEA ENGINEERING DESIGN MASTER CLASS WITH ANSYS WORKBENCH
Wk5 – Wk6: COURSE MODULES - Module 1: Fundamentals of Finite Element Analysis (FEA) Simulation – Mathematical Theory
- Module 2: Introduction to ANSYS Workbench Simulation & Analysis Interface
- Module 3: Basic Steps in Building Numerical Engineering Simulation Model
- Module 4: ANSYS Static & Structural Thermal & Computational Fluid Dynamics (CFD) Analysis Hands On Workshops
TECHNICAL WORKSHOPS - CADDAS 003a: Static Structural Analysis
- CADDAS 003b: Modal Analysis
- CADDAS 003c: Eigen Buckling Analysis
- CADDAS 003d: Harmonic Response Analysis
- CADDAS 003e: Magnestostatic Analysis
- CADDAS 003f: Random Vibration Analysis
- CADDAS 003g: Response Spectrum Analysis
- CADDAS 003h: Rigid Dynamic Analysis
- CADDAS 003i: Steady State Thermal Analysis
- CADDAS 003j: Thermal Electric Analysis
- CADDAS 003k: Transient Structural Analysis
- CADDAS 003l: Transient Thermal Analysis
- CADDAS 003m: Heat Transfer & Fluid Flow Analysis
- CADDAS 003n: Computational Fluid Dynamics (CFD) Analysis
CADDAS 004: OFFSHORE FIXED STRUCTURES DETAILED DESIGN MASTER CLASS WITH SACS
Wk7 – Wk8: COURSE MODULES - Module 1A: Offshore Production Jacket Platform Structural Modeling & Simulation Theory based on API RP 2A
- Module 1B: Offshore Production Jacket Platform Structural Modeling & Simulation with SACS
- Module 1B1: Fixed & Floating Offshore Structures Theory
- Module 1B2: Offshore Production Jacket Platform Structural Modeling & Simulation with SACS
- Module 1B3: Starting SACS Executive and Setting up Working Environment
- Module 1B4 Case Study: Structural Modeling of Jacket, Pile and Conductor via Definition Wizard
- Module 1B5 Case Study: Offshore Production Jacket Platform Structural Modeling of Horizontal Frames
- Module 1B6 Case Study: Offshore Production Jacket Platform Structural Modeling of Deck Frames – Cellar & Main Decks
- Module 1B7 Case Study: Offshore Production Jacket Platform Structural Modeling of Joint Connection Design
- Module 1C: Offshore Production Jacket Platform Topside Design Theory Based On API-RP2
- Module 1D: OFFSHORE Production Jacket Platform Environmental Load Analysis with SACS
- Module 1E: Offshore Production Jacket Platform In Place Analysis Theory Based On API-RP2
- Module 2B: Offshore Production Jacket Platform Gravity Load / Weight Analysis Theory based on API RP 2A
- Module 2B: OFFSHORE Production Jacket Platform Gravity Load / Weight Analysis with SACS
- Module 3: Offshore Production Jacket Platform Static Analysis with Non Linear Foundation with SACS
- Module 4: Offshore Production Jacket Platform Basic Static Analysis
- Module 5: Offshore Jacket Single Pile Analysis For Subsea Or Offshore Structures – SACSST005 (OPTIONAL)
REFERENCE LECTURES
MODULE 1: LOADS ON OFFSHORE STRUCTURES - Lecture 1.0: Loads on Offshore Structures
- Lecture 1.1: Loads on Offshore Structures
- Lecture 1.2: Loads on Offshore Structures
- Lecture 1.3: Loads on Offshore Structures
- Lecture 1.4: Loads on Offshore Structures
- Lecture 1.5: Loads on Offshore Structures
- Lecture 1.6: Loads on Offshore Structures
MODULE 2: CONCEPTS OF FIXED OFFSHORE PLATFORM DECK AND JACKET - Lecture 2.0: Concepts of Fixed Offshore Platform Deck and Jacket
- Lecture 2.1: Concepts of Fixed Offshore Platform Deck and Jacket
- Lecture 2.2: Concepts of Fixed Offshore Platform Deck and Jacket
- Lecture 2.3: Concepts of Fixed Offshore Platform Deck and Jacket
- Lecture 2.4: Concepts of Fixed Offshore Platform Deck and Jacket
MODULE 3: STEEL TUBULAR MEMBER DESIGN - Lecture 3.0: Steel Tubular Member Design
- Lecture 3.1: Steel Tubular Member Design
- Lecture 3.2: Steel Tubular Member Design
- Lecture 3.3: Steel Tubular Member Design
- Lecture 3.4: Steel Tubular Member Design
MODULE 4: TUBULAR JOINT DESIGN FOR STATIC & CYCLIC LOADS - Lecture 4.0: Tubular Joint Design for Static & Cyclic Loads
- Lecture 4.1: Tubular Joint Design for Static & Cyclic Loads
- Lecture 4.2: Tubular Joint Design for Static & Cyclic Loads
- Lecture 4.3: Tubular Joint Design for Static & Cyclic Loads
- Lecture 4.4: Tubular Joint Design for Static & Cyclic Loads
- Lecture 4.5: Tubular Joint Design for Static & Cyclic Loads
- Lecture 4.6: Tubular Joint Design for Static & Cyclic Loads
- Lecture 4.7: Tubular Joint Design for Static & Cyclic Loads
- Lecture 4.8: Tubular Joint Design for Static & Cyclic Loads
- Lecture 4.9: Tubular Joint Design for Static & Cyclic Loads
- Lecture 4.10: Tubular Joint Design for Static & Cyclic Loads
- Lecture 4.11: Tubular Joint Design for Static & Cyclic Loads
MODULE 5: TUBULAR JOINT DESIGN FOR STATIC & CYCLIC LOADS - Lecture 5.0: Jackup Rigs Analysis & Design
- Lecture 5.1: Jackup Rigs Analysis & Design
- Lecture 5.2: Jackup Rigs Analysis & Design
- Lecture 5.3: Jackup Rigs Analysis & Design
- Lecture 5.4: Jackup Rigs Analysis & Design
- Lecture 6.0: Design Against Accidental Loads
- Lecture 6.1: Design Against Accidental Loads
- Lecture 6.2: Design Against Accidental Loads
- Lecture 6.3: Design Against Accidental Loads
- Lecture 6.4: Design Against Accidental Loads
- Lecture 6.5: Design Against Accidental Loads
- Lecture 6.6: Design Against Accidental Loads
- Lecture 6.7: Design Against Accidental Load
CADDAS 005: ONSHORE, OFFSHORE & SUBSEA PIPELINE ENGINEERING DESIGN MASTER CLASS WITH CEASAR II
Wk9 – Wk11: COURSE MODULES - Module 1: Fundamentals of Pipeline Engineering for Engineers
- Module 2: Fundamentals of Offshore Pipeline Engineering
- Module 3: Fundamentals of Subsea Pipeline Engineering Design
- Module 4: Pipe & Flowline Project Engineering – FEED / Construction & Installation
- Module 5: Onshore & Offshore Subsea Pipeline Ancillary Equipment
- Module 6: Onshore & Offshore Subsea Pipeline Cathodic Protection Design
- Module 7: Onshore & Offshore Subsea Pipeline Failure – External Corrosion
- Module 8: Onshore & Offshore Subsea Pipeline Performance Requirements
- Module 9: Fundamentals of Piping & Pipeline Engineering Detailed & FEED Design
- Module 10: Onshore & Offshore Pipeline Stress Analysis with CEASAR II
- Module 11: CAESAR II Static Load Case Editor Theory
TECHNICAL WORKSHOPS - CADDAS 005.1a: Onshore Pipe Stress Analysis with CAESAR II
- CADDAS 005.1b: Fundamentals of Fatigue Analysis of Piping System using CAESAR II
- CADDAS 005.1c: Theoretical Methodology of Piping System Fatigue Analysis with CAESAR II
- CADDAS 005.1d: Case Study Piping System Fatigue Analysis using CAESAR II
- CADDAS 005b1: CEASAR II Onshore & Offshore Stress Analysis Of Gas Transmission Pipeline (Buried & Unburied) Hands On Training For Intermediate Onshore, Offshore & Subsea Pipeline Engineer (Optional)
- CADDAS 005c1: CEASAR II Stress And Fatigue Analysis Of Offshore Steel Catenary Riser (SCR)Hands On Training For Intermediate Offshore & Subsea Pipeline Engineer (Optional)
CADDAS 006: SUBSEA CONTROLS, HYDRAULICS, SURFS & SUBSEA STRUCTURES INSTALLATIONS MASTER CLASS
Wk12- Wk14: COURSE MODULES - Module 1: Subsea Controls & Systems Hydraulic Sizing
- Module 2: Extended Brown Field Tie Back Development & Field Hydraulic Sizing Workshop
- Module 3: Engineering of Subsea Umbilical & Controls
- Module 4: FEED & Detailed Design & Verification of Subsea Umbilicals, Risers & Flowlines (SURFs)
- Module 5: Subsea Seperation Engineering Technology
TECHNICAL WORKSHOPS - CADDAS006a1:Deepwater Dynamic Umbilical Design
- CADDAS 006a: Verification of Flexible Riser Design Workshop
- CADDAS 006b: Subsea Structures & Installation Calculations Workshop
- CADDAS 006c: Subsea Manifold Structural Design, Verification, and Validation
CADDAS 007: SUBSEA & HYDRODYNAMIC ENGINEERING (MOORINGS, RISER, SUBSEA INSTALLATION, CALM BOUY, STINGER) SIMULATION ANALYSIS MASTER CLASS WITH ORCAFLEX Wk15 – Wk17: COURSE MODULES - Module 1: Introduction to Floating Systems, Riser & Hydraulic Engineering
- Module 2: Introduction to ORCAFLEX Analysis & Simulation Programme
TECHNICAL WORKSHOPS - CADDAS 007a: FPSO Drift & Excursion Practical Calculation Workshop
- CADDAS 007b: Free Hanging Catenary Riser from an FPSO
- CADDAS 007c: FPSO Single Point Mooring
- CADDAS 007d: Riser Installation - Pull In Analysis
- CADDAS 007e: Lay On Tower Analysis
CADDAS 008: SUBSEA FLOW ASSURANCE & ASSET INTEGRITY MANAGEMENT & IMPLEMENTATION FROM FIELD LIFE CYCLE PERSPECTIVE MASTER CLASS Wk17 – Wk20: COURSE MODULES - Module 1: Introduction to Subsea Flow Assurance
- Module 2: Subsea and Deepwater Flow Assurance Challenges & Insulation
- Module 3: Onshore & Subsea Flow Control in Oil & Gas Wells and Pipelines
- Module 4: Subsea Systems Flow Assurance & Operability
- Module 5: Pre Commissioning, Hook Ups & Decommissioning of FPSO’s & Offshore Structures
- Module 7: Asset Integrity Management Approach to achieve Excellence in Design & Process Safety
TECHNICAL WORKSHOPS - CADDAS 008a: Workshop on Asset Integrity Management of a Typical Gas Processing Plant
- CADDAS 008b: FPSO & Associated Subsea System Facilities Asset Integrity Assessment and Management with Case Study
- CADDAS 009c: Flexible Pipe (SURFS) Fatigue & Service Life Assessment For Asset Integrity Management – Case Study
- CADDAS 009d: Pipeline Fatigue & Service Life Assessment For Asset Integrity Management – Case Study
Wk17 – WK 20: Group or Individual Project, Competence Assessment & Certifications
TRAINING CERTIFICATION
Issued directly by Chess Subsea Engineering Europe
To be certified by OPITO and City & Guilds internationally; please note that certification fees and online assessment apply.
Core assessment areas & certifications to be awarded by OPITO and City & Guilds are as follows:
- Subsea Technology
- Subsea Equipment and Tools
- Material Technologies, Subsea Systems and Flow Assurance
- Subsea Controls
- ROV Systems
Kindly contact us directly on
info@chesssubseaengineering.com TRAINING METHODOLOGY All the trainings & workshops are interactive and include the following training methodologies as a percentage of the total tuition hours:-
15% Lectures
5% Workshops & Work Presentations
75% Case Study Software Hands On & Competence Assessments
5% Videos & General Discussions
TRAINING MODE: ONLINE | OFFLINE (IN HOUSE) – PORTHARCOURT ONLY No 5 Ken Saro Wiwa Street, Off Rumoula Link Road, Rivers State, Portharcourt, Nigeria
NB: Training at client’s office within Nigeria also available for a minimum of eight (8) staffs. Please contact us directly on
trainings@chesssubseaengineering.com for quote.
IN HOUSE & OFFLINE TRAINING MODE: Two (2) days intensive training followed by practical intensive real time engineering design case study as project. Competence to be accessed weekly globally online and offline.
COURSE TRAINING DATES Start Date Offline: 5th October 2018
Start Date Offline: 3rd December 2018
Start Date Offline: 4th February 2019
Start Date Offline: 6th May 2019
Start Date Online: Any Time
COURSE FEES Offline: N 675,000 only @ our facilities in Portharcourt Only)
Online: N455, 000 Naira Only
PORTHARCOURT (OFFLINE ONLY) No 5 Ken Saro Wiwa Street, Off Rumoula Link Road, Rivers State, Portharcourt, Nigeria
HOW TO REGISTER: Contact
trainingnigerians@chesssubseaengineering.com for registration booklet
For all inquiries please call +447946739882, +447903310642, + 2348151453146, +2348139340494
Or send an email to: trainings@chesssubseaengineering.com ,
trainingnigerians@chesssubseaengineering.com ,
info@chesssubseaengineering.com BANK ACCOUNT DETAILS All payment with regards to trainings should be made to the following account below:
AFRICA:
CHESS SUBSEA ENGINEERING AFRICA, NIGERIA
FIRST BANK OF NIGERIA PLC
ACCOUNT NO: 2031711533 (CURRENT) INTERNATIONAL:
CHESS SUBSEA ENGINEERING EUROPE LIMITED
BARCLAYS BANK
SORT CODE: 20-45-45
ACCOUNT NO 50328731
SWIFTBICBARCGB22
IBANGB03 BARC 2045 4550 3287 31
BRANCH: BARCLAYS BANK PLC, 90-93 BROAD ST, READING RG1 2AP
PHONE: 0345 734 5345 For our other international courses globally or engineering projects executed worldwide; please kindly visit
www.chesssubseaengineering.com
No comments:
Post a Comment